Recycling plastic waste
You wish to recycle :
LPDE plastic films
All kind of plastics
Experts in recycling since 2015, we support you from their collection at source until their recycling in our French factories.
We offer an extensive recycling service and guarantee their recycling within our certified network of experts throughout France and Europe
A unique recycling technology
Discover our latest innovation: B.Clear. Installed at Reborn Pyrenees in 2021, B.Clear is equiped with a unique technology allowing to remove the ink printed on polyethylene films.
The objective: upcycling a quality usually recycled in products with low added value.
Quality assets
The Reborn Lab
1.5M€ invested in a new generation equipment
We systematically test the material on 10 criteria, in order to guarantee mechanical and aesthetic qualities similar to a brand new product.
1. Differential Scanning Calorimetry
2. Melt Flow Index
3. Density
4. Humidity
5. Infrared Spectro
6. Ash
7. Rigidity
8. Friction
9. Shrink
10. Sealing
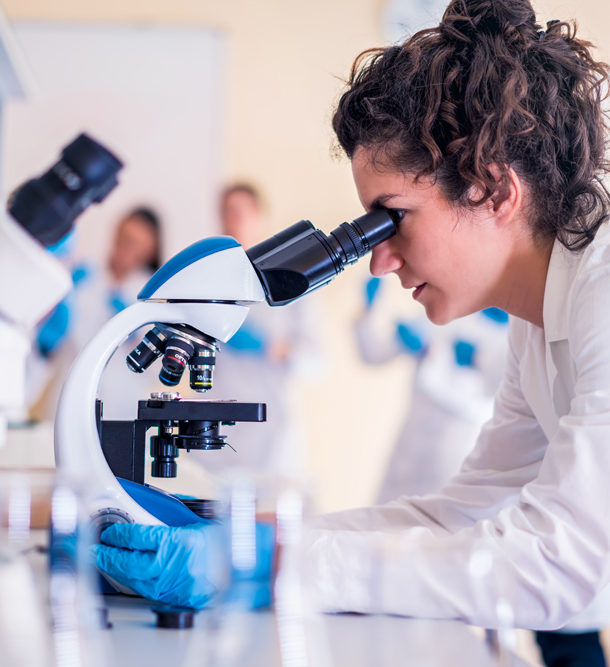
Logistics expertise,
recycling at the best cost
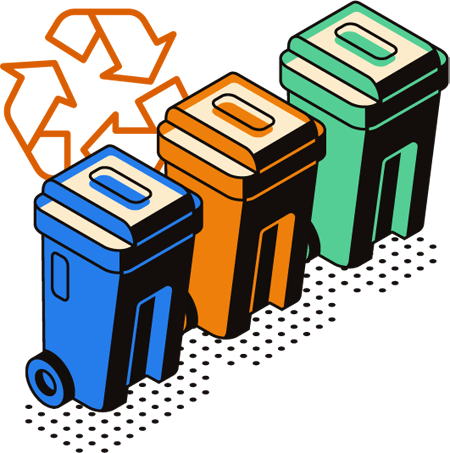
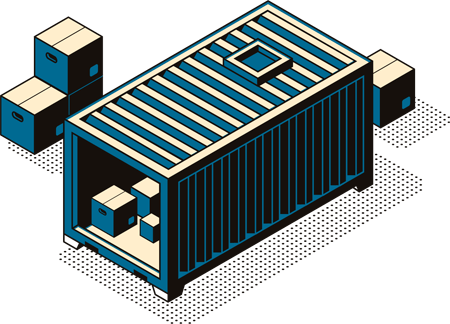
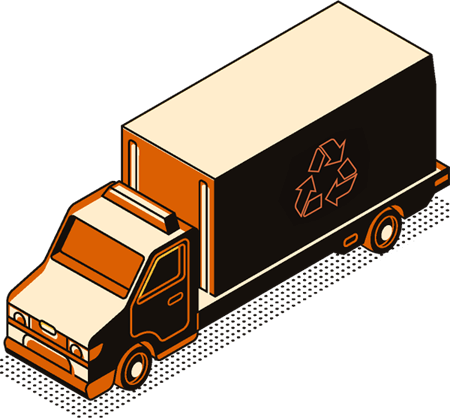
The sorting allows both to better valorize all the recoverable waste and to avoid their degradation by protecting them from bad weather and pollution from organic waste.
We help you to set up this sorting on site and to train the concerned operators.
- On-site installation of balers by quality European baler suppliers
- A ½ day support for the installation of the machines
- Up to 4 times more material stored in the same space due to improved bale compaction ranging from 100 to 500 kg
- Significant savings in transportation and space costs
Our transporters are experts in waste management.
They are present all over Europe to minimize the cost and environmental impact of waste transportation.
1. Find your recurring lots or offer new ones
2. Make your pickup requests in 1 click
3. Follow the evolution of your batch
4. Access all necessary documents in one place
Extended recycling service : making sure everything is recycled
100% of the waste we collect of is recycled
- 0kg buried
- 0kg exported
- 0kg incinerated
For two years, reborn's extended recycling service has :
- gained the confidence of 70 industrial sites and distribution platforms
- recycled 10 000T per year of plastics and papers and aim at recycling 50 000T in 5 years
Expertise in plastics processing since 1962 and in recycling since 2015.
From waste to packaging : welcome in the smartcycle
STEP 1
- Install a balling press if needed
- Train teams on sorting at source
- Collect industrial waste
STEP 2
- Recycle mechanicaly LPDE films in our French factories
- Send other types to our recycling partners
STEP 3
Transform recycled material into recyclable premium packaging
- Carlsberg's packaging is produced with 30% of their own waste
Legal compliance

Our sites are certified and conform according to International standard ISO 14001.
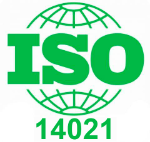
The waste collected are certified according to the hierarchy described by International standard ISO 14021.
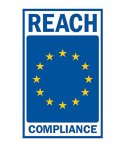
Waste is only collected within the European Union and Switzerland. They are certified in accordance with the European REACH regulation.
If you wish to obtain a certificate of compliance with the Californian Act or other non-european normative repositories
FAQ
The acronym LDPE stands for Low Density Polyethylene, It differs from HDPE (High Density PolyEthylene) by a lower density, which gives it more flexibility and less rigidity. It is the most widely used material in packaging in Europe.
IT is usually a flexible, transparent or printed film, however it is very difficult to recognize LDPE from any other type of plastic. The best way to know what material you are dealing with is to look at the recycling pictogram printed on each package. Polyethylene is listed using the number 4.
Contrary to popular belief, LDPE is recyclable. When the material is well sorted, clean and isn't printed on too much, it is possible to recycle it mechanically to transform for a new usage of the same quality.
The mixing of materials makes mechanical recycling impossible without seriously compromising the quality of the recyclable material. This is why it is very important to separate the packaging according to the material it is made from, so that it can be transformed into new products. It is also preferable to create only packaging that is "single-material" and to avoid producing so-called "complex" or "multi-layer" packaging (= several materials mixed together) for the same reason.
Unlike chemical recycling which is extremely energy intensive, mechanical recycling requires very few resources. It takes place in 4 main stages: the collected films are reduced to flakes in a mechanical shredder, then sent to a washer in order to remove any residual dust or other matter. They are then dried at room temperature in a large blower, before being heated just to 122°C to form new, ready-to-use granules. Note that the water is also at room temperature and reused in a closed loop after filtration, which allows us to minimize consumption. Mechanical recycling is therefore a very simple process that does not consume many natural resources, which significantly improves the carbon impact of packaging made from this recycled material!
The EFSA (European Food Safety Authority) does not yet accept recycled polyethylene packaging having direct contact with food. The first steps towards this have been made with the authorization for PET. Polyethylene and polypropylene should follow from 2023 depending on the progress of research into the sterilization of the material.
Yes, the LDPE we recycle is fully compliant with ISO 14001 and ISO 14021 standards, as well as with REACH authorizations which set out the materials authorized on the European market. The recycled LDPE that we produce is free from SVHCs such as phthalates or heavy metals.
Mechanical recycling of LDPE is a very simple process that uses very little water and energy. Chemical recycling, however, (high technology) emits more CO2 during the recycling of a plastic than the emissions from oil or gas extraction intended to produce the same plastic.
Reborn® mechanically recycled LDPE packaging guarantees the same properties and barriers as non-recycled LDPE packaging (barrier to moisture, dirt, resistance to weight and stretching), while producing half the carbon emissions.
We use the PEF developed by the EU.
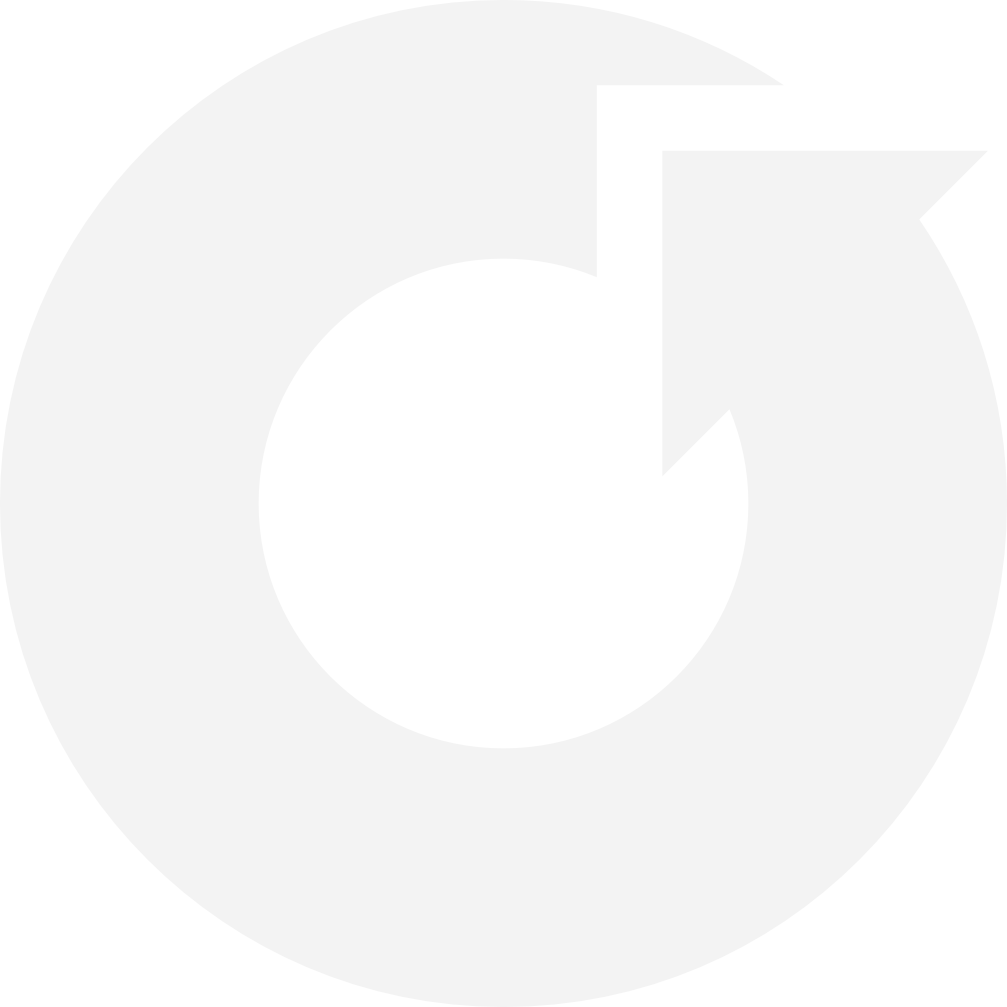